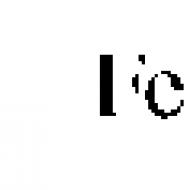
Четырёхосевая обработка на станке с поворотной осью. Конструкция портала и вертикальной оси Z гравировально-фрезерного станка с ЧПУ Самодельная поворотная ось
После рассмотрения вариантов конструкции длинной оси - X - можно перейти к рассмотрению оси Y. Ось Y в виде портала - наиболее популярное решение в сообществе хоббийных станкостроителей, и неспроста. Это простое и вполне рабочее, хорошо себя зарекомендовавшее, решение. Однако, и в нем есть подводные камни и моменты, которые надо уяснить перед проектированием. Для портала крайне важна устойчивость и правильный баланс - это снизит износ направляющих и передач, снизит прогиб балки под нагрузкой, уменьшит вероятность подклинивания при перемещении. Для определения правильной компоновки посмотрим на силы, приложенные к порталу во время работы станка.
Рассмотрите схему хорошенько. На ней отмечены следующие размеры:
- D1 - расстояние от области резания до цента расстояния между направляющими балки портала
- D2 - расстояние между приводным винтом оси X до нижней направляющей балки
- D3 - расстояние между направляющими оси Y
- D4 - расстояние между линейными подшипниками оси X
Теперь рассмотрим действующие усилия. На картинке портал перемещается слева направо за счет вращения приводного винта оси X(расположен внизу), который приводит в движение гайку, зафиксированную снизу на портале. Шпиндель опущен и фрезерует заготовку, при этом появляется сила противодействия, направленная навстречу движению портала. Эта сила зависит от ускорения портала, скорости подачи, вращения шпинделя и силы отдачи с фрезы. Последняя зависит от собственно фрезы(типа, остроты, наличия смазки и т.п.), скорости вращения, материала и прочих факторов. Определению величины отдачи с фрезы посвящено множество литературы по подбору режимов резания, в настоящее время нам достаточно знать, что при движении портала возникает сложносоставная сила противодействия F. Сила F, приложенная к зафиксированному шпинделю, по конструктивным элементам прикладывается к балке портала в виде момента A = D1 * F. Данный момент может быть разложен на пару равных по модулю, но разнонаправленных сил A и B, приложенных к направляющим #1 и #2 балки портала. По модулю Сила А = Сила B = Момент А / D3. Как отсюда видно, силы, действующие на направляющие балки уменьшаются, если увеличивать D3 - расстояние между ними. Уменьшение сил снижает износ направляющих и крутильную деформацию балки. Также, с уменьшением силы А, уменьшается и момент B, приложенный к боковинам портала: Момент B = D2 * Сила A. Из-за большого момента B боковины, будучи не способными согнуться строго в плоскости, начнут виться и изгибаться. Момент B необходимо уменьшать также потому, что необходимо стремиться к тому, чтобы нагрузка всегда распределялась по всем линейным подшипникам равномерно - это снизит упругие деформации и вибрации станка,а, значит, повысит точность.
Момент B, как уже было сказано, можно уменьшить несколькими путями -
- уменьшить силу A.
- уменьшить плечо D3
Задача - сделать силы D и C сделать как можно более равными. Эти силы складываются из пары сил момента B и веса портала. Для правильного распределения веса надо рассчитать центр масс портала и разместить его точно между линейными подшипниками. Именно этим объясняется распространенная зигзагообразная конструкция боковин портала - это сделано для того, чтобы сместить направляющие назад и приблизить тяжелый шпиндель к подшипникам оси X.
Итого, при проектировании оси Y учитывайте следующие принципы:
- Старайтесь минимизировать расстояние от приводного винта/рельсов оси X до направляющих оси Y - т.е. минимизируйте D2.
- Снижайте по возможности вылет шпинделя относительно балки, минимизируйте расстояние D1 от области реза до направляющих. Оптимальным ходом по Z обычно считается 80-150 мм.
- Снижайте по возможности высоту всего портала - высокий портал склонен к резонансу.
- Рассчитывайте заранее центр масс всего портала, включая шпиндель и разрабатывайте стойки портала таким образом, чтобы центр масс располагался точно между каретками направляющих оси X и как можно ближе к ходовому винту оси X.
- Разносите направляющие балки портала подальше - максимизируйте D3 для снижения момента, приложенного к балке.
КОНСТРУКЦИЯ ОСИ Z
Следующим шагом является выбор структуры наиболее важной части станка - оси Z. Ниже приведены 2 примера конструктивного исполнения.
Как было уже упомянуто, при строительстве станка с ЧПУ необходимо учитывать силы, возникающие при работе. И первым шагом на этом пути является отчетливое понимание природа, величины и направления этих сил. Рассмотрим схему ниже:
Силы, действующие на ось Z
На схеме отмечены следующие размеры:
- D1 = расстояние между направляющими оси Y
- D2 = расстояние вдоль направляющих между линейными подшипниками оси Z
- D3 = длина подвижной платформы(базовой пластины), на которую собственно монтируется шпиндель
- D4 = ширина всей конструкции
- D5 = расстояние между направляющими оси Z
- D6 = толщина базовой пластины
- D7 = вертикальное расстояние от точки приложение сил реза до середины между каретками по оси Z
Посмотрим на вид спереди и отметим, что все конструкция перемещается вправо по направляющим оси Y. Базовая пластина выдвинута максимально вниз, фреза заглублена в материал и и при фрезеровке возникает сила противодействия F, направленная, естественно, противоположно направлению движения. Величина этой силы зависит от оборотов шпинделя, числа заходов фрезы, скорости подачи, материала, остроты фрезы и т.п.(напоминаем, что некоторые предварительные расчеты того, какие материалы будут фрезероваться, а значит, и оценка сил реза, должна быть сделана перед началом проектирования станка). Как влияет данная сила на ось Z? Будучи приложена на расстоянии от места, где закреплена базовая пластина, эта сила создает крутящий момент А = D7 * F. Момент, приложенный к базовой пластине, через линейные подшипники оси Z передается в виде пар поперечных сил на направляющие. Силы, преобразованная из момента, обратно пропорциональная расстоянию между точками приложения - следовательно, для снижения усилий, изгибающих направляющие, необходимо увеличивать расстояния D5 и D2.
Расстояние D2 также участвует в случае фрезерования вдоль оси X - при этом возникает аналогичная картина, только возникающий момент приложен на заметно большем рычаге. Этот момент старается провернуть шпиндель и базовую пластину, а возникающие силы перпендикулярны плоскости пластины. При этом момент равен силе реза F, умноженной на расстояние от точки реза до первой каретки - т.е. чем больше D2, тем меньше момент(при неизменной длине оси Z).
Отсюда следует правило: при прочих равных надо стараться обязательно разнести каретки оси Z подальше друг от друга, особенно по вертикали - это значительно увеличит жесткость. Возьмите за правило никогда не делать расстояние D2 меньше 1/2 длины базовой пластины. Также убедитесь, что толщина платформы D6 достаточна, чтобы обеспечить желаемую жесткость - для этого необходимо рассчитать максимальные рабочие усилия на фрезе и смоделировать прогиб пластины в САПР.
Итого , придерживайтесь следующих правил при конструировании оси Z портального станка:
- максимизируйте D1 - это снизит момент(а следовательно, силы), действующий на стойки портала
- максимизируйте D2 - это снизит момент, действующий на балку портала и ось Z
- минимизируйте D3(в пределах заданного хода по Z)- это снизит момент, действующий на балку и стойки портал.
- максимизируйте D4(расстояние между каретками оси Y) - это снизит момент, действующий на балку портала.
С числовым программным управлением, повышающий производственные особенности рабочего инструмента. Она позволяет обрабатывать нестандартные заготовки, изготовляя изделия сложной формы. Оборудование дает возможность осуществления полноценной 3D и 4D обработки на станках с ЧПУ. Чаще всего агрегат используется для работы с деревом, но он может обрабатывать и другие материалы.
Особенности
Поворотные оси характерны не для каждого станка. Основная задача данного элемента – обеспечить вращение заготовки вокруг своей оси. С его помощью выполняется обработка заготовок, в основе которых лежит:
- дерево;
- алюминиевые, цветные и медные сплавы;
- пластик.
За работу оси отвечает двигатель. Она может быть частью оригинальной конструкции станка, или же устанавливается отдельно. При отдельной установке элемент выступает в качестве четвертой оси.
Четырехосевая обработка в отличие от трехосевой имеет ряд преимуществ. Трехосевой способ дает возможность выполнить 3D обработку с одной стороны заготовки, поскольку другая будет прикреплена к столу. Чтобы обработать вторую сторону, приходится выполнять дополнительные действия по переустановке изделия. Поворотная ось позволила решить эту проблему. С ее помощью заготовку можно обработать со всех сторон без дополнительных действий.
Благодаря этой особенности можно получить изделия, имеющие сложную конструкцию:
- мебельные комплектующие;
- ювелирные изделия;
- декоративные деревянные узоры.
Станки с поворотной осью широко распространены при оформлении декора. Правильная настройка прибора позволит обеспечить обработку в автономном режиме. Заготовки будут схожими с изделиями ручной работы.
Конструкция
Существуют различные варианты станков с поворотной осью. Наиболее качественными являются . На обычных приборах производительность более низкая.
На высокопроизводительных агрегатах устанавливается ременная передача. Некоторые модели оснащены пятой осью. Размеры рабочего стола могут варьироваться, но ширина и длина не должна быть меньше одного метра. Аппараты самодельного типа характеризуются установкой на поворотную ось токарного патрона или планшайбы. На заводских приборах распространены трехкулачковые токарные патроны.
Наиболее популярным типом двигателя является двухфазный на четыре провода.
Габариты и стоимость оборудования зависят от конкретной модели. Крупногабаритные варианты применяются в промышленных условиях. Более компактные модели можно использовать для бытовых задач и малого бизнеса. Но даже самые дешевые варианты смогут позволить себе далеко не все. Поэтому многие изготовляют ЧПУ станок самостоятельно.
Станок с поворотной осью своими руками
Неопытным пользователям не рекомендуется делать станок с поворотной осью из металла. Первоначально следует попробовать сделать агрегат из фанеры. На первом этапе составляется чертеж и управляющая фрезерная программа. Этот этап можно выполнить при помощи сервиса Rhinoceros. Толщина фанеры должна составлять не менее 15 миллиметров. Ее необходимо закрепить на столе, после чего станок с ЧПУ сделает нужные заготовки.
Второй этап заключается в сборке полученных деталей. После этого необходимо приобрести подшипник водяного насоса. Данный элемент продается в магазинах автозапчастей. Перед установкой подшипника детали необходимо покрыть лакокрасочным веществом. Подшипник можно укрепить при помощи болтов. Для работы прибора потребуется группа комплектующих, в числе которых:
- стол для станка;
- ременная передача;
- шаговый двигатель.
Дополнительные детали изготовляются на токарном станке. После того, как сборка агрегата будет выполнена, потребуется отдельно докупить драйвер, отвечающий за управление шаговым двигателем. Новый драйвер необходимо поставить в блок управления станком.
Перед тем, как сделанная своими руками поворотная ось ЧПУ, будет запущена, нужно убедиться, что комплектующие хорошо закреплены.
Использование
Существуют два способа работы с поворотной осью:
- индексный;
- непрерывный.
Первый способ предполагает пошаговую обработку, начиная со свободных движений, и заканчивая неподвижными условиями. Переход от одной обработки к другой сопровождается остановкой и фиксацией. Для второго способа осуществлять дополнительные действия не требуется. Исправная обработка зависит от наличия программы и подходящей модели рабочего инструмента.
Для полноценной обработки станок должен быть обеспечен четырехкоординатной системой управления. Чтобы компенсировать вес шпинделя, ось Z оборудована газовой пружиной.
Основы эффективного программирования
Работа с осью вращения (4-ой координатой)
Нередки случаи, когда на трехкоординатный станок с ЧПУ дополнительно монтируют управляемый поворотный стол (делительную головку). Управляемый поворотный стол – это устройство, которое способно поворачивать закрепленную в нем деталь на требуемый угол по определенной команде. Обычно 4-ая ось управляется при помощи адресов А или В, а числовое значение определяет угол поворота в градусах.
Рис. 10.4. Управляемые поворотные столы HAAS
Существуют два варианта работы с управляемым поворотным столом. Первый вариант – нам просто необходимо повернуть его на определенный угол и затем выполнить какую-либо технологическую операцию (индексация). Второй вариант – нужно выполнить фрезерование одновременно с поворотом стола. В этом случае мы имеем синхронное линейное перемещение исполнительного органа станка по трем (или менее) координатам с вращением стола. При этом СЧПУ станка должна поддерживать данный вид интерполяции.
Для управления поворотным столом достаточно в кадр с линейной интерполяцией, позиционированием или постоянным циклом добавить адрес А (В):
- G00 X_Y_Z_A_ – позиционирование;
- G01 X_Y_Z_A_F_ – линейная интерполяция.
Типичный формат для работы с постоянным циклом:
G81 Х0 Y0 Z-5 А0 F45 R0.5
А15
А30
А45
G80
Программирование 4-ой оси не должно вызвать у вас особых трудностей. Прос то нужно учесть несколько технических особенностей при работе с управляемым поворотным столом. Во-первых, поворотный стол может вращаться как в положительном, так и в отрицательном направлении. Направление вращения и соответствующий знак определяются по правилу правой руки. Во-вторых, поворот стола может быть запрограммирован как в абсолютных, так и в относительных координатах. В-третьих, у многих станков существует ограничение на числовое значение угла поворота. Например, вам нужно повернуть стол на 400°, а СЧПУ позволяет указывать угол не более 360°. Придется запрограммировать дополнительный кадр с углом в 40° относительно предыдущего положения стола. Ну и напоследок учтите, что чем дальше мы удалимся от центра вращения, тем большей будет ошибка линейного перемещения.
Следующие примеры помогут вам понять, как программируется дополнительная ось вращения. В первом случае необходимо просверлить отверстия на периферии диска. Во втором случае нужно получить винтовую канавку на поверхности вала, используя одновременное линейное перемещение фрезы и вращение поворотного стола.

Рис. 10.5. Требуется просверлить 4 отверстия на периферии диска, закрепленного в кулачках поворотного стола. Чтобы просверлить такие отверстия, нужно поворачивать стол через 90°

Рис. 10.6. Необходимо получить винтовую канавку на поверхности вала. Вал закреплен в кулачках управляемого поворотного стола. Самый простой способ обработки такой канавки – расчет при помощи CAD/САМ-системы
% O0001 N100 G21 N102 G0 G17 G40 G49 G80 G90 N104 T1 M6 N106 G0 G90 G54 X-16.612 Y0. A-2.993 S1000 M3 N108 G43 H1 Z125.171 M8 N110 Z35.605 A-10.578 N112 G1 Z33.932 A13.459 F200. N234 G0 Z123.253 A3.674 N236 M5 N238 G91 G28 Z0. M9 N240 G28 X0. Y0. A0. N242 M30 % |
Часть вторая:
Часть третья:
Часть четвертая:
Часть пятая:
Часть шестая: электроника станка
Ну и отдельный плюс - это линейные подшипники сразу в корпусе, так как их проще устанавливать на самодельные конструкции. Простые LM08UU дешевле, но под них требуется сделать держатель (можно напечатать на принтере) - это отдельный разговор.
Итак, несколько слов про сам набор комплектующих для новой оси Y, затем про доработку. Получил посылку спустя 3 недели после заказа, в почтовом пакете и картонной узкой коробке для прочности. Это плюс, просто из пакета у меня цилиндрические валы выпадают, на Али почему то об этом продавцы не задумываются. А зря.
Каждая номенклатура из комплекта упакована отдельно в пакетик. В подшипниках присутствуют следы масла
Для оценки масштаба приложил к направляющим и винту линейку. Линейка на 30 см, железо на 40 см
Торцы винта и валов без заусенцев. Такое ощущение, что валы нарезают в стандартные размеры от большого хлыста, так как заметно чуть чуть нагара на торце. Но обработано после отрезки. В принципе, ту же самую операцию я могу провести самостоятельно, поэтому стараюсь брать как можно длиннее отрезки.
На торцах сделана фаска. Если отрезаете самостоятельно (а я подрезаю немного в размер), то фаску можно снять на точиле/вручную. Она в основном декоративная, чтобы не было заусенцев и при установке подшипников не задевало за шарики.
Микроны не ловил, диаметр вала вполне 8 мм. К точности изготовления цилиндрических валов вопросов нет, главное чтобы не погнули при доставке. У меня больше претензии к подшипникам. Взял на Али несколько лотов дешевых LM08UU, так вот некоторые сидят внатяг, а некоторые слегка люфтят. На подшипниках это заметно сильно, особенно если на один и тот же вал установить.
Суппорты SK8 удобная штука. Устанавливаются сразу на профиль (любой), и зажимается вал. При желании, можно использовать в любительских конструкциях, для зажима чего угодно с диаметром 8мм (например, центра для станка).
Габаритные и установочные размеры найти не проблема, они стандартные. Если требуется - пишите в личку или смотрите в первых двух темах, там были чертежи.
Первоначально при примерке конструкции и до заказа использовал 3Д печатные суппорты. Сейчас удалил из за ненадобность. С металлическими получается гораздо жё
стче конструкция
Суппорты-подшипники KP08 для фиксации ходового винта. Для зажима есть два винта под шестигранник на 1,5.
Данные суппорты очень удобно использовать в любительских конструкциях: их применяют в 3Д принтерах для оси Z, а также можно сделать самодельные ременные передачи, зажав отрезок вала 8мм в этом подшипнике и установив на вал шестерню. Обратите внимание: для установки установки винта Т8 на пластину на оси X в данной копии CNC2417 используются подшипники KFL08, в виде фланца.
Ну и последнее - корпусной линейный подшипник SC08UU. Стоит чуть дороже(раза в два) простого LM08UU, но в нем присутствует резьба М4 для установки крепежный винтов. Также очень удобно использовать в любительских конструкциях из-за простоты установки. Есть вариант SC08LUU, удлиненный, который у меня используется в слайдере оси Z.
Про комплект все, теперь про доработку.
Начал сборку с осей X и Y, ну и кареток соответственно.
Для начала собираем ось Y: двигатель, суппорт, винт с гайкой и муфта.
Устанавливаем двигатель на держатель. Все просто: четыре винта М3. Длина небольшая, в основном зависит от используемой пластины (толщина) и шайб.
Двигатель с пластиной перед установкой на профиль.
Далее устанавливаем KP08 напротив, выдерживая расстояние от центра оси двигателя и от центра оси суппорта одинаковым
Далее устанавливаем суппорты вала SK8, четыре штуки, по паре на один вал. При установке валов не забываем про подшипники.
Далее собираем пластину с двигателем X, а также пластину с суппортом KFL08
Пластины сделаны симметричными, причем можно собрать с обоих сторон винт на KFL08, предварительно установив двигатель на (M3 Brass Spacer - удобно брать наборами).
Изначально был 3Д печатный KFL08, но пока собирал и тестировал успел заказать и получить нормальный)))
Собираем дальше ось Х. Устанавливаем пластины на раму
Устанавливаем вторую пластину.
Пластины обеспечивают дополнительную жесткость конструкции, одновременно являются держателем оси Х. Для усиления использовано 3 цилиндрических вала 8 мм.
Далее в отверстия пластин устанавливаем валы (три штуки) плюс подшипники SC08UU (три пары соответственно)
Фотография поближе. По 10 мм цилиндрического вала с каждой стороны зажимаются в суппорт SHF08. И желательно оставить около 20 мм ходового винта для установки ручки (ручное перемещение каретки).
Устанавливаем пластину-каретку Х на подшипники. Не забываем про гайку. Я использовал 3Д печатный держатель гайки. Купить держатель достаточно проблематично. Из вариантов купить есть или сразу плоскую пластиковую гайку (POM) с отверстиями для крепления (варианты и ). Видел в продаже , но деньгам стоят дорого. Так что пока печатный держатель…
Проверяем свободный ход каретки от начала до конца оси, затягиваем винты.
На пластину уже крепится слайдер оси Z. Можно сделать их отрезка профиля 2080 и суппортов SK8, можно изготовить самостоятельно, можно
Поворотная ось предназначена для обеспечения поворота деталей на требуемый угол. Она представляет собой поворотный механизм, который позволяет осуществлять вращение заготовки в необходимом направлении и под определенным углом. 4 поворотная ось может быть использована для обработки заготовок из таких материалов, как пластик и дерево. Кроме того, ось применяют и для гравировки металлов. Поворотная ось для фрезерного станка ЧПУ позволяет создавать изделия различной сложности: с ее помощью можно изготавливать балясины, ручки, элементы декора с гравировкой, разнообразные статуэтки и другие сложные формы.
Существуют поворотные оси на ременном и гармоническом редукторе. В чем состоит их различие? Первый вариант больше подходит для обработки пластика и дерева, а второй – для работы с твердыми материалами, в частности, с металлом. Кроме того, оси подразделяются на 3-х и 4-х кулачковые. Ось первого типа предназначена для центровки заготовок, которые имеют круглую форму, а 4-х кулачковая ось – для заготовок прямоугольного сечения.
Преимущества поворотной оси для фрезерного станка,
Какие преимущества дает поворотная ось ? Эта деталь значительно расширяет возможности станков с ЧПУ: благодаря позиционированию заготовки в пространстве, становится доступным изготовление сложных изделий. Применение поворотной оси решает проблему автоматизации выполняемых работ: после ее установки обработка заготовок начинает осуществляться в автоматическом режиме. Кроме того, поворотная ось чпу позволят существенно сократить время на изготовление изделия. И, безусловно, поворотная ось делает работу на станке с ЧПУ не только более быстрой, но и более комфортной: после установки оси исчезает необходимость перестановки заготовки, поскольку для обработки потребуется закрепить ее только один раз. Важно отметить, что установка поворотной оси не вызывает сложностей: как правило, оси подходят для любых станков, а стандартные программы позволяют подключение данных устройств, поэтому перенастраивать их не понадобится.
Таким образом, поворотная ось ЧПУ для станков дает возможность в максимально короткие сроки изготавливать качественные изделия, требующие высокой точности. Соответственно, установка поворотной оси позволит существенно повысить производительность и увеличить прибыль.