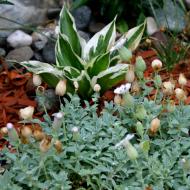
Классификация повреждений и дефектов, обнаруженных на трубопроводах. Допустимые размеры дефектов труб, подлежащих ремонту сваркой Отводы от магистрального трубопровода
6) разнотолщинность листов;
Рассмотрим подробную классификацию дефектов стенки МТ с описанием, характеристикой и причиной появления дефекта (табл.2.). а) дефекты механического происхождения; б) дефекты коррозионного происхождения; в) технологические дефекты; г) дефекты сварки (табл.2).
Дефекты стенки трубы В данной классификации дефекты стенки трубы группируются по видам: а) б) в) г)
Перечень опасных участков магистральных трубопроводов.
Степень опасности каждого участка т\п зависит от изменения его проектного положения, наличия дефектов в стенке труб и формы их сечения, нарушения состояния изоляции т\п и систем ЭХЗ. На основании рез-тов изучения тех.документации и натурного обследования т\п д.составляться перечень потенциально опасных участков, к кот.относят:
1. участки имеющие сложную конфигурацию,
2. участки примыкающие к площадочным сооружениям со стороны высокого давления,
3. пересечение с искусственными сооружениями и препятствиями,
4. подводные переходы,
5. учаскти пересечения с др. т\п-ми
6.участки с высоким уровнем грунтовых вод,
7. участки на которых имели место отказы сопровождающиеся разрушением трубопровода.
8. участки расположенные в ВМГ,
9. участки с температурой перекачиваемого продукта ниже 0°.
пересечения водотоков и водоемов (реки, водохранилища, каналы и др.);
участки, проложенные надземно;
Отводы от магистрального трубопровода.
Линейная запорная арматура, включая вантузы, площадки и укрытия.
Узлы и оборудование для пропуска внутритрубных очистных и дефектоскопических средств.
Узлы редуцирования давления.
Подготовка ТП к пропуску внутритрубных дефектоскопических снарядов. Требования к геометрии ТП и очистке внутренней поверхности.
Подготовка газопровода к пропуску внутритрубных инспекционных снарядов требует проведения ряда организационных и технических мероприятий, выполнение которых позволит произвести запуск и прием внутритрубного инспекционного снаряда, обеспечит безопасное движение его внутри трубы и получение наиболее достоверных данных о состоянии линейной части трубопровода.
Очистку трубопровода от грязи, металлических и посторонних предметов.
Установление реального минимального проходного сечения трубопровода путем пропуска снаряда-калибра.
Устранение крутоизогнутых колен, имеющих радиус изгиба менее преодолеваемого используемыми Исполнителем внутритрубными снарядами, и мест критического сужения проходного сечения трубы; минимальный радиус изгиба и минимальное сужение, позволяющее использовать применяемые для инспектирования внутритрубные инспекционные снаряды, определяются их конкретным типом и оговариваются при заключении договора на диагностическое обследование.
Проведение ревизии надземных переходов и их опор и при необходимости их усиление.
Проведение обследования трассы на наличие утечек и устранение их до начала работы по пропуску внутритрубных инспекционных снарядов.
Определение необходимого количества и мест расстановки шурфуемых или нешурфуемых маркеров, которые должны быть расставлены вдоль трассы газопровода строго над осью трубы.
Для пропуска внутритрубных снарядов устанавливается камера пуска приема размером который позволяет размещать наибольшие снаряды. Для пропуска дефектоскопа min r изгиба т\п должен быть равен 3D т\п. Min скорость потока перекачиваемой жидкости 3 м/с.
Задвижки должны быть полнопроходными с конструктивным входом и выходом. Перед пуском снаряда необходимо проверить открытие всех задвижек.
Обратные клапаны должны быть разработаны с учетом своевременного прохождения снаряда. Идеальный вариант – использование клапанов имеющих истройство для захвата тарелки во время прохождения снаряда. Перед запуском дефектоскопа в т\п необходимо провести подготовительные работы: 1. выявить возможные зоны сужения т\п и устранить их, 2. очистить полость трубопровода от загрязнений особенно от парафина и предметов застрявших в задвижках,
3. пропустить прибор для измерения геометрии т\п обеспечивающий выявление таких повреждений как вмятина и гофр. Участок т\п по которому будет проходить дефектоскоп должен быть отсечен от отводов резервных ниток,
4. необходимо проверить состояние камеры пуска приема скребка,
5. очистку т\п необходимо провести с качеством 1 кг парафина на 100 км т\п.
Классификация дефектов трубопроводов.
Дефекты металла и стенки трубы различного происхождения, к ним относятся:
1) внутренние дефекты – внутренние разрывы, расслоения, растрескивания (трещины), грубозернистость структуры;
2) наружные дефекты проката (металлические дефекты) – закаты, оксиды, пленка, корочка (окалина), пережог, пористость, усадочные раковины;
3) коррозия – атмосферная, межкристаллическая, поверхностная, газовая;
4) металлургические дефекты сварного шва;
5) механические повреждения поверхности;
6) разнотолщинность листов;
7) разностенность: прессовых, тянутых профилей – в поперечном направлении; труб сварных – в продольном направлении.
Дефекты стенки трубы В данной классификации дефекты стенки трубы группируются по видам: а) дефекты механического происхождения (царапины, риски, надрезы); б) дефекты коррозионного происхождения (1сплошная коррозия: равномерная, неравномерная; 2местная: точечная, пятнами, язвы; 3питтинговая коррозия; 4межкристаллическая)в) технологические дефекты (Трещины, расслоения, рванины, закаты, клепы); г) дефекты сварки (1.брызги, капли застывшего металла;2. прижог, законтачивание; 3. дефекты в кольцевых и продольных сварочных соединниях).
а – дефект на трубе; б – механическая обработка дефекта; в – схема изложения сварных швов; 1 – наплавочный слой; 2 – заполняющие слои; 3 – контурный шов;
4 – облицовочный шов.
Ремонту сваркой подлежат трубы, имеющие отдельно расположенные единичные дефекты, которыми считаются дефекты, имеющие расстояние между собой:
ü не менее 300 мм при максимальном размере дефекта менее или равном 35 мм;
ü не менее 500 мм при максимальном размере дефекта от 35 до 60 мм.
При этом количество дефектов на один погонный метртрубы не должно превышать двух.
Ремонту сваркой не подлежат следующие дефекты на трубах:
ü дефекты, размеры которых превышают значения, приведены в табл. 9.7; коррозионные каверны и
ü раковины, расположенные на соединительных узлах и деталях;
ü дефекты, расположенные на расстоянии менее 300мм от продольных и кольцевых сварных швов;
ü дефекты, имеющие трещины или видимое расслоение металла, а также расположенные на вмятинах. Заварка дефектов на трубах выполняется ручной электродуговой сваркой электродами основного типа.
Перед заваркой дефект обрабатывается механическим способом (шлифовальной машинкой или фрезой) с целью (рис. 9.9.б):
· получения формы кратера, обеспечивающего равномерное и качественное положение металла;
· полного удаления продуктов коррозии и возможных поверхностных микротрещин.
Прилегающие к кратеру участки зачищаются до металлического блеска на ширину не менее 15 мм с предварительным удалением остатков изоляционного покрытия, ржавчины, грязи, масляных пятен.
Подогрев металла труб перед сваркой устанавливается согласно табл. 9.8.
Таблица 9.8
Предварительный подогрев металла труб
Подогрев труб осуществляется, как правило, электрическими или газовыми нагревателями. Контроль температуры выполняется приборами типа ТП-1.
Заварка дефектов труб с пределом прочности от 42 до 55 кгс/мм 2 производится с использованием электродов марок УОНИ 13/55, «Гарант», LВ52A(И) диаметром 2,5¸4,0 мм, заварка дефектов труб с пределом прочности 55-57 кгс/мм 2 – электродами марок «Шварц 3К», ВСФ-60 или аналогичных.
Наплавка металла на дефект включает: первый наплавочный слой, заполняющие слои, контурный шов, облицовочный шов (рис. 9.9.в). Первый наплавочный слой и контурный шов выполняются электродами диаметром 2,5¸3,25 мм, заполняющие и облицовочный – электродами диаметром 3,0¸4,0 мм на сварочных режимах, приведенных в табл. 9.9.
Таблица 9.9
Режим заварки дефектов
При заварке дефектов количество направляемых слоев должно составлять не менее двух (без учета контурного слоя шва). Сварка выполняется валиками шириной не более 20мм с взаимным перекрытием не менее3 мм. Контурный слой шва выполняется с колебаниями перпендикулярно к граничной линии (рис. 9.9.г), при этом ширина данного шва , составляет от 8 до 14 мм. Сварные швы накладываются плотно с мелкой чешуйчатостью (0,5¸0,7 мм), что обеспечивает плавный переход к основному металлу трубы.
![]() |
После завершения заварки дефектного участка трубы наружная поверхность наплавки обрабатывается механическим методом, при этом поверхность должна быть ровной, без видимой чешуйчатости, усиление – равномерным по всей площади. Высота усиления должна находиться в пределах от 0,7 до 1,5мм (рис. 9.10) и контролироваться с помощью индикатора.
Рис. 9.10. Механическая обработка наплавленного участка
Таким образом, производится сварка (заварка) одиночных каверн.
Групповыми кавернами считается скопление каверн не менее 10 на 100 см 2 поверхности трубы.
При диаметре и глубине групповых каверн, заметно ослабляющих стенку трубы, часть стенки трубы с кавернами вырезается и на ее место вваривается заплатка заподлицо с поверхностью трубы, .
Заплатка для вварки заподлицо с поверхностью труб изготавливается овальной формы из труб с толщиной стенок, равной толщине стенок ремонтируемого газопровода, из стали той же марки или с такими же физико-механическими характеристиками. Размеры заплат должны быть шириной не более 250мм (по кольцу трубы), но не более половины диаметра трубы, и длиной не более 350 мм (по оси). Минимальный размер заплат: ширина – 100 мм, длина – 150 мм (по тем же направлениям). Во всех случаях между длиной и шириной заплаты должна быть разница в пределах 50¸100 мм.
Размеры ввариваемых заплат при ремонте газопроводов различных диаметров приведены в табл. 9.10.
Таблица 9.10
Размеры ввариваемых заплат
Края ввариваемых заплат обрезаются со скосом кромок. Отверстие в трубе вырезается по форме заплаты также со скосом кромок. На кромках заплаты и отверстия делается притупление. Для обеспечения полного провара заплаты ввариваются с подкладными кольцами (рис. 9.11.а).
Подкладное кольцо изготавливается из листовой стали толщиной 3¸4 мм и шириной 20¸30 мм и приваривается к заплатке с внутренней стороны так, чтобы его края выступали за края заплаты на 10¸12 мм. Зазор между кромками заплаты и трубы для обеспечения провара должен составлять 2¸5 мм. Заплата заваривается электродами типа УОНИ 13/55. При толщине заплаты до 12 мм сварной шов заваривается в три слоя. Корень шва выполняется электродами диаметром 3 мм, последующие слои – электродами диаметром 3¸4 мм. Сварка выполняется обратно – ступенчатым швом по всему периметру заплаты в три-четыре ступени (рис. 9.11.б). Для прижатия заплаты к трубе на время прихватки используются устанавливаемым над отверстием приспособлением, представляющим собой П-образную скобу с винтом посередине, снабженным захватным устройством. На заплате для этого также приваривается маленькая скоба.
Рис. 9.12. Схема расположения надрезов и заплат:
А =В =С =500 мм; D =1500 мм; L =9360 мм
расстояние между концентраторами по периметру – 200 мм
Для исследований была отобрана труба диаметром 820 и толщиной стенки 9 мм, изготовленная из стали 19Г и находившаяся в эксплуатации 27 лет, со следующими характеристиками:
ü продольные напряжения s т = 407 МПа, s вр =555 МПа;
ü поперечные напряжения s т = 456 МПа, s вр = 557 МПа.
На наружную поверхность трубы было нанесено 5 одинаковых надрезов: с длиной – 200; глубиной – 3,5 и шириной 3 мм. Схема нанесения надрезов показана на рис. 9.12.
Для приближения к условиям эксплуатации трубу подвергли гидравлическим испытаниям в циклическом режиме. Размах циклов составлял: P min = 2,0 МПа; P max = 4,0 МПа.
Анализ состояния трубы проводился поэтапно после выдержки под нагрузкой в 200 циклов.
Надрез №5 был заверен до начала испытаний последовательно на каждом этапе заваривался один надрез, вырезалось окно размером 150´200 мм и вваривалась заплата. После 600 циклов были заварены четыре надреза (№№ 2,3,4,5) и вварены заплаты №№ 6,7,8. Затем трубу подвергли нагрузке в 5000 циклов, после чего надрез №1 был вырезан и вместо него была вварена заплата. Последовательность ремонта надрезов и вварки заплат приведена в табл. 9.11.
Приобретая трубы для своих надобностей, каждый покупатель имеет право потребовать у продавца сертификат качества, в котором приведены данные о партии труб, стали и производителе. Там же может содержаться информация о проведенных испытаниях.
Это очень важная информация, которая дает нам понять, что труба не только произведена в соответствии с ГОСТом или ТУ, но еще и испытана на прочность и наличие дефектов различного типа.
Для проведения этих испытаний используется различное оборудование. Но испытывать можно не только новые трубы, но и трубы, находящиеся в составе трубопроводов и даже буровых установок.
Прибор выявляет такие изъяны, как:
- нарушение сплошности;
- ужимы;
- непровары;
- закаты;
- трещины;
- волосовины;
- рванины;
- неметаллические включения.
Использование труб с перечисленными дефектами может привести к возникновению техногенных катастроф и аварий. Дефекты возникают как при плохой настройке производственного оборудования, так и использовании некачественного сырья.
Вихретоковый дефектоскоп можно легко встроить в действующие производственные линии. Он позволяет проводить контроль изделия прямо в процессе его изготовления, что значительно снижает расходы на отбраковку некачественной продукции.
В основе метода лежит анализ взаимодействия внешнего электромагнитного поля с магнитным полем, производимым вихревыми токами, которые наводятся в контролируемом изделии при помощи возбуждаемой катушки. При этом контроль проводится без взаимодействия с исследуемой трубой, что позволяет сохранять технологическую скорость производственной линии.
Оборудование для поиска дефектов в действующих трубопроводах или установках
Это способ базируется на использовании двух пар акустических датчиков. Один их датчиков каждой пары улавливает продольные колебания, а второй – поперечные.
Обработка сигналов, поступивших от датчиков во время проведения испытаний, позволяет достаточно точно определить характер и расположение имеющихся дефектов. Этот способ используется для трубопроводов, имеющих диаметр более 80 мм и толщину стенки в пределах 5 – 15 мм.
Дефекты, которые надежно обнаруживаются предлагаемым методом:
- локальное уменьшение толщины стенки трубы до 50% от первоначальной;
- дефекты сварных швов;
- серия язв (с их простиранием вдоль оси трубы более 100 мм);
- раскрытие даже самых малых трещин.
Дефектоскопия бурильных труб необходима по той причине, что при бурении газовых и нефтяных скважин нередко происходят аварии, связанные с разрушением конструктивных элементов бурильной колонны.
Самыми уязвимыми местами колонны являются с замками (сварные и резьбовые).
Эти разрушения образуются вследствие возникновения усталости металла и чаще всего представляют собой трещины.
Контроль резьбовых участков труб производится с помощью передвижной комплексной дефектоскопической установки типа ПКДУ-1. Трубы контролируют при помощи выносных датчиков, соединенных с пунктом контроля кабелями длиной до 60 м.
Неразрушающий контроль тела стальных насосно-компрессорных труб производится установкой ДИНА-1. Ее работа основана на магнитноиндукционном методе.
Толщину стенок
алюминиевых и стальных бурильных труб, насосно-компрессорных установок и проверяют с помощью толщинометра БУИТ-1. Его действие основано на измерении временного промежутка между импульсами ультразвука, отраженными от внутренней и наружной стенки трубы. При этом не нет необходимости очищать поверхность труб от ржавчины и краски, так как ввод ультразвука производится бесконтактным способом.
Это лишь малая часть приборов, используемых для проверки целостности как производимых, так и уже работающих труб. Обычному потребителю эти приборы чаще всего недоступны, поэтому его задачей является визуальный осмотр труб при их покупке и проверка прилагаемого к ним сертификата. Трубы для своего хозяйства лучше приобретать в больших проверенных магазинах строительных товаров. Там вероятность купить заведомо некачественный товар гораздо меньше.