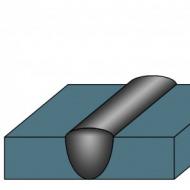
Строительство и оборудование индивидуального домастолярные, каменные, кровельные работы. Как правильно варить электросваркой без опыта Электрододержатель со штоковым фиксатором
Сварочные швы — участки сварного соединения, образующие в результате кристаллизации (затвердевания) расплавленного металла или в результате пластической деформации при сварке давлением или сочетания кристаллизации и деформации.
Разделение понятий сварочное соединение и сварочный шов необходимо потому, что последний, как связующая часть соединяемых элементов, определяет геометрическую форму, сплошность, прочность и другие свойства металла непосредственно в месте сварки.
Определяются свойствами металла самого шва и зоны основного металла, прилегающего к шву, с измененной структурой и во многих случаях с измененными свойствами зоны термического влияния. Необходимо учитывать и некоторую часть основного металла, прилегающую к зоне термического влияния и определяющую концентрацию напряжений в месте перехода от металла шва к основному металлу и пластических деформаций в зоне термического влияния, что отражается на характере и распределении усилий, действующих в сварном соединении.
Критерии для классификации
Сварочные швы подразделяются в зависимости:
— от формы сечения;
— от характера сопряжения свариваемых деталей;
— по внешнему виду;
— по выполнению;
— по количеству слоёв;
— по числу проходов;
От протяжённости;
— по направлению действующего усилия;
— по положению в пространстве;
— по назначению;
— от условий работы сварного изделия;
— по способу удержания расплавленного металла;
— по виду сварки;
— по применяемому для сварки материалу.
Классификация
В зависимости от формы сечения сварочные швы могут быть:
стыковыми; угловыми; прорезными (электрозаклепочными).
В зависимости от характера сопряжения свариваемых деталей различают следующие виды сварных соединений:
— стыковые соединения;
— угловые соединения;
— тавровые соединения;
— нахлесточные соединения;
— торцовые соединения.
Сварочные швы по внешнему виду подразделяются на:
— нормальные (плоские)
— выпуклые (усиленные)
— вогнутые (ослабленные).
Выпуклый сварной шов Нормальный сварной шов Вогнутый сварной шов
Выпуклые сварные швы лучше работают при статических (постоянных) нагрузках, однако они неэкономичны. Нормальные и вогнутые швы лучше подходят при динамических и знакопеременных нагрузках, поскольку за счет более плавного перехода от основного металла к сварному шву снижается вероятность возникновения концентрации напряжений, приводящих к разрушению шва.
По выполнению сварочные швы могут быть односторонними и двусторонними.
Односторонний шов Двухсторонний шов
По количеству слоев сварка бывает однослойной и многослойной, по числу проходов сварные швы бывают однопроходные и многопроходные.
Однослойный, однопроходный Многослойный Многопроходный
Многослойный шов используется при сварке толстого металла, а также чтобы уменьшить зону термического влияния.
Проход – однократное перемещение источника тепла в одном направлении при сварке или наплавке. Валиком называется часть металла сварного шва, которая была наплавлена за один проход.
Слой сварного шва – металл шва, состоящий из одного, двух или нескольких валиков, которые размещены на одном уровне поперечного сечения шва. При сварке каждый слой многослойного стыкового шва, кроме усиления и подварочного шва, отжигается при наложении следующего слоя. В результате такого теплового воздействия улучшается структура и механические свойства металла шва.
В зависимости от протяженности сварные швы бывают непрерывными и прерывистыми. Стыковые швы обычно делают непрерывными. Угловые швы могут быть выполнены:
— непрерывными;
— односторонними прерывистыми;
— двусторонними цепными;
— двусторонними шахматными;
— точечными.
По направлению действующего усилия
Согласно этому критерию сварные швы делятся на:
— продольные (фланговые) – направление действующего усилия параллельно оси сварного шва;
— поперечные (лобовые) – направление действующего усилия перпендикулярно оси сварного шва;
— комбинированные – сочетание продольного и поперечного швов;
— косые – направление действующего усилия размещено под углом к оси сварного шва.
По положению в пространстве швы подразделяются на:
По назначению сварочные швы бывают
— прочные;
— плотные (герметичные);
— прочно-плотные.
В зависимости от условий работы сварного изделия швы делятся на:
— рабочие, предназначенные непосредственно для нагрузок;
— нерабочие (связующие или соединительные), используемые только для соединения частей сварного изделия.
По ширине сварные швы подразделяются на
— ниточные с шириной шва равной или незначительно превышающей диаметр электрода, выполняются без поперечных колебательных движений сварочного электрода;
— нормальные с шириной
— уширенные, которые выполняют с поперечными колебательными движениями электрода.
По способу удержания расплавленного металла швы сварных соединений делятся:
— на швы выполненные без подкладок и подушек;
— на съемных и остающихся стальных подкладках;
— на медных, флюсо-медных, керамических и асбестовых подкладках;
— на флюсовых и газовых подушках.
По конфигурации сварного шва:
— прямолинейные;
— кольцевые;
— вертикальные;
— горизонтальные;
По виду сварки швы сварных соединений разделяют на:
— швы дуговой сварки (ГОСТ5264-80);
— швы автоматической и полуавтоматической сварки под флюсом (ГОСТ 8713-79);
— швы дуговой сварки в защитных газах (ГОСТ14771-76);
— швы электрошлаковой сварки (ГОСТ15164 - 78);
— швы электрозаклепочные (ГОСТ14776 - 79);
— швы контактной электросварки (ГОСТ15878 - 79);
— швы газовой сварки;
— швы паяных соединений.
По применяемому для сварки материалу швы сварных соединений подразделяются на сварочные швы:
— углеродистых и легированных сталей (ГОСТ 5264-80; 14771-76; 15164-78; 8713 - 79 и др.);
— соединения цветных металлов (ГОСТ 16038 - 70; 14806 - 69);
— соединения биметалла (ГОСТ 16098 - 70);
— соединения винипласта и полиэтилена (ГОСТ 16310-70).
Самым надежным и прочным способом соединения деталей остается сварочный шов. Без сварки сегодня не может обойтись ни одно производство, применяется она и в быту. Практически каждый домашний умелец обязательно использует сварку.
Конечно, не все умеют правильно сваривать детали, им приходится пользоваться услугами профессиональных сварщиков. Но при большом желании, можно научиться сваривать детали своими руками.
Самой простой считается электросварка. Именно с нее начинается изучение сварочного процесса. Только после приобретения определенного опыта в получении хорошего шва, можно приступать к выполнению сложной работы. Давайте познакомимся с основами сварочного технологического процесса и его нюансами.
Прежде чем начать сварку, детали сначала выправляют и затем хорошо чистят. Причем очищать детали необходимо до начала сборки узла. Появление дефектов сварочного шва обычно связано с различными видами загрязнений:
- Ржавчины;
- Масла;
- Окалины.
Очень важно хорошо зачистить металл там, где будут проводиться сварочные работы. Это касается кромок каждой детали. Любое загрязнение в щели между свариваемыми деталями, должно быть обязательно удалено. Можно выжечь грязь сильным пламенем горелки, продуть мощной струей сжатого воздуха.
Очищать поверхность можно самыми разными способами:
- Щеткой с металлическим ворсом;
- Иглофрезами;
- Гидропескострйными системами;
- Дробью;
- Горелкой;
- Шлифовальным кругом;
- Травлением;
- Растворителем.
После подготовки инструментов и материала, давайте разберемся по шагам как правильно варить электросваркой.
Возбуждение сварочной дуги
Чтобы возбудить дугу, существует несколько способов.
Вариант 1. Сварщик кончиком электрода должен прикоснуться к металлической поверхности, затем быстро отвести его назад на несколько миллиметров (2 – 4). Как результат появится дуга. Её длина поддерживается медленным опусканием электрода. Все зависит от величины расплавления. Перед тем как образуется дуга, лицо работника обязательно должно быть закрыто защитным щитком.
Вариант 2. Возбудить сварочную дугу можно и другим способом. Кончиком электрода сварщик быстро проводит по металлической поверхности, затем также быстро поднимает его на пару миллиметров. Между электродом и поверхностью металлом появится дуга. Во время сварки необходимо стремиться поддерживать очень короткую дугу. Возле шва будут образовываться небольшие капли металла. Плавление электрода будет плавным и спокойным. Шов получается глубоким и прочным.
Если размер дуги будет слишком длинным, основной металл недостаточно хорошо проплавится. Металл электрода при сварке начнет окисляться, появятся сильные брызги. Шов после такой сварки будет неровным, с многочисленными окисными вкраплениями.
Длину дуги можно легко определить по звуку её горения. Если длина имеет стандартные значения, звук будет однотонным и равномерным. Очень длинная дуга начнет издавать резкие звуки, которые будут постоянно сопровождаться сильными хлопками.
Если дуга оборвалась, ее возбуждают снова. Кратер, на котором оборвалась дуга, тщательно заваривают. Если необходимо сварить очень важный узел, который будет эксплуатироваться при знакопеременной нагрузке, а также возможно появление «усталости», категорически запрещается возбуждать дугу прямо на поверхности основного металла. Если возбуждение будет происходить не по шву, возможно появление «ожога» металла. В этом месте шов может просто разрушиться при эксплуатации детали.
Первые шаги
Чтобы научиться, хорошо сваривать детали, сначала практикуются на ненужных металлических валиках. Не требуется создавать соединительные швы, необходимо просто научиться правильно расплавлять материал. Поверхность металла не должна иметь следов ржавчины и быть хорошо очищенной.
Как делаются валики
Электрод вставляется в держатель. Чтобы вызвать появление тока в области плавления, достаточно чиркнуть по поверхности металла кончиком электрода, или просто постучать несколько раз по заготовке.
Когда появится электрическая дуга, электрод направляется на заготовку, с выдержкой постоянного зазора между поверхностью металла и электрической дугой. Зазор должен иметь постоянное значение, и лежать в диапазоне 3–5 миллиметров.
Важно! Чтобы получить качественный шов, необходимо все время поддерживать одинаковую длину дуги. Если изменить эту величину, дуга может прерваться, шов будет иметь много дефектов.
Направление электрода делается под определенным углом относительно плоскости заготовки. Самым оптимальным считается угол в 70 градусов, Наклон не имеет определенного значения, главное чтобы сварщику было удобно. В процессе работы сварщик сам находит для себя оптимальное положение, в зависимости от специфичности выполняемой работы.
Во время таких практических занятий нужно научиться правильно, подбирать силу тока, чтобы подача все время оставалась стабильной. Если тока будет недостаточно, дуга будет постоянно гаснуть. При очень мощном потоке, начнется проплавление металла. Только экспериментальным путем можно научиться, правильно устанавливать режим сварки.
Техника получения хорошего сварного соединения
Когда валики начнут получаться ровными, можно попытаться начать изготавливать соединительные швы. Такую операцию сможет выполнить достаточно опытный практикант, который умеет варить электросваркой.
Зажигание электрода выполняется согласно описанной выше технологии. Единственным отличием будет движение руки сварщика. Она будет выполнять колебательные движения. Расплав будет как бы переходить с одной поверхности детали на другую. Движение может происходить по нескольким траекториям:
- Зигзагообразная;
- Петлевидная;
- Елочкой;
- Серпом.
Для тренировки можно взять небольшую металлическую заготовку. По поверхности мелом провести линию, чтобы ее можно было увидеть через темное стекло маски. Именно по ней нужно двигаться электродом, чтобы получить своеобразный шов, в виде любой вышеуказанной траектории.
После того, как шов остыл нужно молотком отбить шлак и рассмотреть проделанную работу.
Когда появился небольшой опыт можно начинать изготавливать соединительные швы, которые имеют несколько видов:
- Тавровые;
- Стыковые;
- Угловые;
- Внахлест.
Кроме того, такие швы могут быть горизонтальными и вертикальными, могут свариваться в разных направлениях.
Только после многочисленных тренировок можно добиться равномерного движения руки. После этого можно получить красивые детали.
Как продолжить сварку после её остановки?
Так как варить электросваркой длинный шов без остановки невозможно, приходится менять электрод или были другие причины прерывания, то на месте остановки получается небольшое углубление, получившее название: кратер. Для возобновления работы, необходимо выполнить следующие действия:
1.Дуга должна зажигаться не на самом кратере. Необходимо отступить от него 12 мм. Затем ее медленно пододвигают к кратеру.
2.Колебательными движениями тщательно заваривается сам кратер.
3.После этого можно продолжать сварку, выдерживая установленный режим. Для получения надежного соединения, сварка должна иметь несколько слоев:
- Заготовка, толщиной 6 мм – 2 слоя;
- При толщине 6–12 мм – 3 слоя;
- Если толщина металла превышает 12 мм – 4 слоя.
Движение электрода в каждом слое должно быть одинаковым. Сварочный шов, после завершения операции обрабатывают, снимая все излишки.
Как получаются вертикальные швы
На рисунке 69а, показана вертикальная сварка. Так как варить вертикальный шов электросваркой достаточно проблемно из-за того, что капли расплава стремятся упасть, то нужно варить такие швы используют короткую дугу. Поверхностное натяжение не дает каплям сразу скатиться вниз. Они быстрее попадают в кратер.
Кончик электрода убирают от капли, чтобы она стала твердой. Вертикальную сварку нужно начинать снизу, постепенно двигаясь наверх. Нижележащий кратер не даст упасть каплям металла. Смотри рисунок 69в. При работе можно наклонять электрод. Когда его наклоняют вниз, сварщик видит, как распределяются капли в месте разделки шва.
Когда нужно выполнить вертикальную сварку, начинаются с верхней точки, электрод необходимо установить в положение I. Смотри рисунок 69г.
Когда капли начинают опускаться, электрод устанавливается в положение II. Капля не будет стекать, ей не позволит короткая дуга.
Наиболее подходящим диаметром электродов для вертикальной сварки, считаются 3 – 4 мм. Величина тока не должна быть очень высокой, примерно 160 ампер.
Чтобы добиться минимального стекания расплава, когда свариваются горизонтальные швы (смотри рисунок. 70, а), кромки скашиваются у одной верхней детали.
Возбуждение дуги должно происходить на нижнем торце (положение I). Затем дуга переводится на торец верхней детали (положение II). Стекающая капля начинает подниматься.
Как должен двигаться конец электрода, когда выполняется однослойная горизонтальная сварка, можно посмотреть на рисунке 70а, в правой стороне.
Горизонтальные швы разрешается варить в виде продольных валиков. Самый первый должен вариться 4 миллиметровым электродом, а все остальные, диаметром 5 миллиметров.
Это основные нюансы, которые позволят правильно варить вертикальный шов электросваркой.
Как электросваркой сварить потолочный шов
Частый вопрос: как варить потолочный шов электросваркой, ведь он стекает? Ответ прост: такие швы варятся короткой дугой. Сварочный электрод должен иметь тугоплавкое покрытие. Когда происходит сварочный процесс, на торце возникает чехольчик, который не позволяет каплям металла, скатиться вниз. (Смотри рисунок. 70, б). Во время работы конец электрода равномерно удаляют, а потом приближают к свариваемой детали. Когда удаляется, дуга сразу гаснет, шов начинает твердеть. Чтобы выполнить потолочную сварку, независимо от направления, пользуются только электродами малых диаметров. Сила тока уменьшается (10-12%), если сравнивать сварку металла аналогичной толщины, производимой внизу.
Когда свариваются потолочные швы, начинают всплывать пузырьки газа. Они оказываются в самом корне шва. От этого страдает прочность и качество сварного соединения.
Применение потолочной сварки имеет ограниченный характер. О ней вспоминают, когда невозможно получить шов из нижнего положения.
Как варятся угловые швы
Расплавленный металл при этой сварке, будет стекать вниз. Оптимальным способом сварки подобных швов из нижнего положения, считается «в лодочку». Деталь устанавливается таким образом, чтобы не происходила течь шлака прямо перед дугой. (Смотри рисунок. 68, а).
Когда сваривается угловой шов, при горизонтальном расположении нижней плоскости, иногда плохо провариваются вершины угла.
Причиной образования такого непровара может стать начало сварочного процесса с листа, стоящего вертикально. Расплавленный металл начинает стекать вниз, на лист, не успевший хорошо прогреться. Именно поэтому варить такие швы нужно с нижней плоскости. Причем дуга должна зажигаться в определенной точке (А). Движение должно осуществляться согласно схеме рисунка 68 б.
Электрод наклоняется под 45 градусов, по отношению к свариваемым деталям. Во время сварки нужно электрод немного наклонять в разные стороны. (Смотри рисунок 68 в).
Если угловые швы варятся не «в лодочку», сварка делается однослойной, с катетом шва менее 8 мм. Если величина катета превышает это значение, выполняют несколько слоев.
Для сварки нескольких слоев углового шва, нужно сначала создать узкий валик. Для этого пользуются 3-4 мм электродом. Такой диаметр позволяет полностью проварить корень.
Чтобы определить количество проходов, учитывают размер площади поперечного сечения, имеющегося шва. Обычно эта величина равна 30-40 кв. миллиметров. Рисунок 68 г наглядно показывает, как должны выглядеть угловые швы с разным количеством слоев, имеющие разделку кромок, полностью проваренные.
Как варятся стыковые швы
Если кромки не имеют скосов, накладываемый валик должен иметь небольшое расширение с каждой стороны стыка. Чтобы не допустить непровара, требуется создать равномерное распределение расплавленного металла.
Только правильная установка тока и грамотный подбор электродов, позволит хорошо проварить 6 миллиметровый металл, если детали не имеют скоса кромок. Величина тока подбирается опытным путем. Для чего сваривается несколько пробных планок.
Если детали имеют V-образные скосы, стыковая сварка может быть однослойной или иметь несколько слоев. Главную роль в этом вопросе играет толщина металла.
Когда варится один слой, возбуждение дуги должно происходить в пункте «А», на границе скоса, согласно рисунку 67а. После чего электрод опускают вниз. Полностью проваривается корень шва, затем дугу отправляют на следующую кромку.
Когда электрод движется по скосам, его движение специально замедляют, чтобы обеспечить хороший провар. На корне шва, наоборот ускоряют движение, чтобы не допустить сквозного прожога.
На обратной стороне сварочного соединения, профессионалы советуют накладывать дополнительный подварочный шов.
В некоторых случаях на противоположную сторону шва монтируют стальную 2-3 миллиметровую подкладку. Для этого повышают сварочный ток, примерно на 20–30% относительно стандартной величины. Сквозное проплавление в данном случае полностью исключается.
Когда создается валик шва, стальная подкладка также приваривается. Если она не мешает конструкции изделия, ее оставляют. При сварке очень важных конструкций, делается проварка противоположной стороны корня шва.
Если нужно сварить стыковой многослойный шов, вначале проваривается корень шва. С этой целью используют электроды, диаметром 4–5 миллиметров. Затем выполняется наплавка следующих слоев расширенными валиками, для чего используются электроды больших размеров (Смотри рисунки 67, б, в).
Подбор сварочных электродов
Чтобы правильно выбрать подходящий электрод, необходимо учесть несколько важных параметров:
- Толщину заготовки;
- Марку стали.
В зависимости от вида электрода подбирается значение силы тока. Сварка может выполняться в самых разных положениях. Нижняя подразделяется на группы:
- Горизонтальная;
- Тавровая.
Сварка вертикального типа может быть:
- Снизу вверх;
- Потолочная;
- Тавровая,
Каждый производитель в инструкции к электродам, обязательно сообщает значение сварочного тока, при котором они будут нормально работать. В таблице показаны классические параметры, применяемые опытными сварщиками.
На величину силы тока оказывает влияние пространственное положение, а также величина зазора. К примеру, чтобы работать с 3 миллиметровым электродом, сила тока должна достигать 70–80 ампер. Таким током можно пользоваться для выполнения потолочной сварки. Этого будет достаточно для сварки деталей, когда величина зазора намного превосходит диаметра электрода.
Чтобы варить снизу, при отсутствии зазора и соответствующей толщине металла, разрешается для обыкновенного электрода установить силу тока в 120 ампер.
Для определения силы тока берется 30–40 ампер, которые должны соответствовать одному миллиметру диаметра электрода. Другими словами, для 3 мм электрода нужно установить ток 90-120 ампер. Если диаметр равен 4 мм, сила тока будет равна 120–160 амперам. Если выполняется вертикальная сварка, сила тока уменьшается на 15 %.
Для 2 мм устанавливается примерно 40 – 80 ампер. Такую «двойку» всегда считают очень капризным.
Существует мнение, что если диаметр электрода имеет малые значения, значит с ним очень легко работать. Однако это мнение ошибочно. К примеру, чтобы работать с «двойкой» нужна определенная сноровка. Электрод быстро горит, он начинает сильно греться при установке большого тока. Такой «двойкой» можно варить тонкие металлы при малом токе, но необходим опыт и большое терпение.
Электрод 3 — 3.2 мм. Сила тока 70–80 Ампер. Сварка должна проводиться только на постоянном токе. Опытные сварщики считают, что выше 80 ампер, невозможно выполнить нормальную сварку. Это значение годится для резки металла.
Сварку нужно начинать с 70 Ампер. Если увидите, что невозможно проварить деталь, добавьте еще 5-10 Ампер. При непроваре в 80 ампер, можно установить 120 ампер.
Для сварки на переменном токе можно установить силу тока 110-130 ампер. В некоторых случаях устанавливают даже 150 Ампер. Такие значения характерны для трансформаторного аппарата. При сварке инвертором, эти значения намного ниже.
Электрод 4 мм. Сила тока 110-160 Ампер. В данном случае разброс, равный 50 амперам зависит от толщины металла, а также вашего опыта работы. «Четверка» также требует особого мастерства. Профессионалы советуют начинать со 110 ампер, постепенно увеличивая силу тока.
Электрод 5 миллиметров и больше. Такие изделия считаются профессиональными, их используют только профи. В основном их применяют для наплавки металла. В сварочном процессе они практически не участвуют.
Зачем прокаливают электроды
Это делается только с одной целью, удалить влагу. При сварке сырым электродом, возможно появление дефектов сварочного шва. Такой электрод будет все время липнуть к детали.
В каждой строительной компании обязательно установлено оборудование, которое прокалывает электроды. Такая операция недоступна сварщикам-любителям.
Если вы начали работать с новой пачкой, но не смогли израсходовать ее до конца, оставшееся количество электродов нужно спрятать в сухое и теплое место. Никогда не храните электроды в подвале и на чердаке. Они быстро отсыреют и придут в негодность.
Заключение
Правила сварки достаточно просты, стоит лишь несколько раз потренироваться на ненужном куске железа. Главное следуйте всем приведенным инструкциям и у вас точно все получится. Сможете варить дуговой сваркой и на потолке и на стене.
Сварка многослойных швов
Угловые швы (13.6) формируются за счет вводимого в ванну металла электрода, заполняющего угол между свариваемыми деталями (внешняя часть шва), и расплавленного основного металла (внутренняя часть шва). Определяющими параметрами углового шва являются: катет внешней части К, глубина проплавления s, расчетная величина h, ширина е, толщина И, коэффициент формы шва е/И. При ручной дуговой сварке сечение шва образуется в основном за счет его внешней части, поэтому расчетная величина h-OJK. Если в чертежах указано требование полного провара таврового шва, это может быть достигнуто при толщине примыкающей части не более 8 мм или путем разделки примыкающей части и выполнения шва в несколько проходов. Угловые швы удобнее сваривать «в лодочку».
Сварка многослойных швов имеет свои особенности. После сварки каждого слоя необходимо тщательно очищать его от шлака, а затем сваривать следующий слой. Первый корневой слой заваривают электродами диаметром 3-4 мм, а последующие слои - электродами большего диаметра (5-6 мм). Последний слой служит выпуклостью и одновременно термообрабатывает предыдущие слои, что улучшает качество металла шва. Многослойный шов можно сваривать широкими слоями на все сечение разделки (13.7, а) или отдельными валиками, заполняющими каждый слой шва {рис, 13.7,6). Последний способ применяют чаще, так как он обеспечивает надежное проплавление всего сечения шва.
Важным элементом многослойного шва является подварочный шов, который выполняют после тщательной зачистки или даже удаления части корневого шва, где наиболее вероятно скопление дефектов. Это делают с помощью рубильного молотка крейцмейселем путем вышлифовки абразивным кругом или выплавкой воздушнодуговым резаком. Качественное выполнение подварочного шва во многом обеспечивает прочность всего сварочного соединения. Иногда подварочный шов выполняют до сварки основного сечения шва.
Необходимо особо тщательно сваривать швы, к которым предъявляется требование непроницаемости (плотности). Даже при толщине металла 3-4 мм их рекомендуется сваривать в 2 слоя с разделкой кромок или без разделки. Это гарантирует непроницаемость швов в конструкциях резервуаров, газопроводов и т. п.
По протяженности сварные швы условно считают короткими при длине до 250 мм, и сваривают их на проход (13.8, а), средними - длиной 250 1000 мм, которые сваривают от середины к краям (рас. 13.8,6), и длинными длиной более 1000 мм, их сваривают обратноступенчатым способом (13.8, в) от середины к краям или разбивая на участки (13.8, г). Обратноступенчатая сварка значительно уменьшает коробление деталей от сварки.
Металл толщиной 20 мм и более сваривают «горкой», «каскадом, «блоками», а при двухсторонней сварке шов разбивают на секции, которые сваривают блоками одновременно два сварщика с двух сторон с небольшим опережением одного сварщика (13.9) над другим. Такой способ обеспечивает естественный подогрев кромок и предохраняет от образования трещин в шве и зоне влияния.
По способу заполнения швов по сечению различают однопроходные, однослойные швы (рис. 27, а), многопроходные многослойные (рис. 27,6) и многослойные (рис. 27, в).
Рис. 27. Сварные швы
Многослойные швы
Если число слоев равно числу проходов дугой, то такой шов называют многослойным. Если некоторые из слоев выполняются за несколько проходов, то такой шов называют многопроходным.
Рис. 28. Схемы заполнения шва при сварке: а - каскадом, б - блоками, в - поперечной горкой: 1 - 12 - слои в шве. I, II, III, IV - ступени шва, S - толщина стыка
Многослойные швы чаще применяют в стыковых соединениях, многопроходные - в угловых и тавровых.
Для более равномерного нагрева металла шва по всей его длине швы выполняют двойным слоем, секциями, каскадом и блоками, причем в основу всех этих способов положен принцип обратноступенчатой сварки (рис. 28).
Двойной слой
Сущность способа двойного слоя заключается в том, что наложение второго слоя производится по неостывшему первому после удаления сварочного шлака: сварка на длине 200 - 400 мм ведется в противоположных направлениях.
Этим предотвращается появление горячих трещин в шве при сварке металла толщиной 15 - 20 мм, обладающего значительной жесткостью.
Многослойная сварка обеспечивает получение шва и прилегающей к нему зоны основного металла с необходимыми механическими свойствами. Это обусловлено, как отмечалось, тепловым воздействием накладываемого валика на ранее наложенный слой металла.
Многослойная сварка ввиду многократного воздействия термического цикла сварки на основной металл в околошовной зоне изменяет строение и структуру зоны термического влияния. При сварке длинными участками после каждого последующего прохода предыдущий шов подвергается своеобразному отпуску.
Многослойная сварка выполняется короткими участками, стыки валиков в различных слоях не должны совпадать. При наложении каждого последующего слоя поверхность предыдущего тщательно очищается металлической щеткой до блеска.
Многослойная сварка обеспечивает хороший провар корня шва и значительно повышает плотность сварного соединения.
Многослойная сварка короткими участками может выполняться секциями, каскадным методом или методом горки.
Многослойная сварка также благоприятно влияет на получение менее хрупкой структуры в сварном соединении.
Многослойная сварка ввиду многократного воздействия термического цикла сварки на основной металл в околошовной зоне изменяет строение и структуру зоны термического влияния. При сварке длинными участками после каждого последующего прохода предыдущий шов подвергается своеобразному отпуску. При сварке короткими участками шов и околошовная зона длительное время находятся в нагретом состоянии. Помимо изменения структур, это увеличивает и протяженность зоны термического влияния.
Форма сварочной ванны в зависимости от ее нагрева. - холодная, б-перегретая, в-нормальная. Многослойная сварка чугуна применяется редко и лишь в тех случаях, когда невозможно поддерживать всю ванну в жидком состоянии.
Двухсторонний шов. Многослойную сварку применяют при сварке толстых листов, когда мощность сварочного аппарата недостаточна для заполнения шва в один проход. Иногда многослойную сварку применяют исходя из технологических соображений. При многослойной сварке необходимо делать разделку кромок.
Многослойную сварку ведут способом каскад. При сварке трубопроводов с толщиной стенки более 6 мм и содержанием углерода в металле более 0 18 % следует применять предварительный подогрев, обеспечивающий во время сварки температуру металла шва в околошовной зоне не ниже 200 С. Стык должен завариваться без перегрева. В случае возникновения перегрева необходимо обеспечить медленное остывание и нагрев перед возобновлением сварки до 200 С. Металл сварочной ванны необходимо поддерживать в густом состоянии, чтобы предотвратить выгорание хрома и молибдена. Рекомендуется предварительный подогрев до 250 - 300 С. Применяется одно - и многослойная сварка с наименьшим числом перерывов. После окончания сварки пламя горелки медленно отводят вверх, что способствует более полному выделению газов из расплавленного металла. Хромомо-либденовые и молибденовые стали подвергают термической обработке.
Двухсторонний шов. Многослойную сварку применяют при сварке толстых листов, когда мощность сварочного аппарата недостаточна для заполнения шва в один проход. При многослойной сварке необходимо делать разделку кромок.
Многослойную сварку выполняют, укладывая три или более электродов в разделку кромок или в угол при положении в лодочку. Ток к электродам подается от нескольких источников. Для устойчивости процесса электроды покрывают стальной накладкой, облицованной слоем листовой меди (рис. IX.9, в), под которую укладывают слой бумаги, предохраняющий накладку от подгорания. При сварке одиночными электродами со стандартным покрытием также необходимо пользоваться указанными накладками.
Многослойную сварку выполняют короткими участками, стыки валиков в различных слоях не должны совпадать. При наложении каждого последующего слоя поверхность предыдущего тщательно очищают металлической щеткой до блеска.
Схемы сварки наклонным (а. Многослойную сварку выполняют, укладывая электроды в разделку кромок или в угол при положении в лодочку. Ток к электродам подают от нескольких источников.
Отжигающий валик. Многослойную сварку элементов толщиной 6 - 15 мм при средней и большой протяженности швов выполняют обратноступенчатым способом, от середины к концам шва. При многослойной сварке каждый предыдущий слой шва как бы отжигается при сварке последующего слоя.
Многослойную сварку элементов толщиной 6 - 15 мм при средней и большой протяженности швов выполняют обратноступенчатым методом, ог середины к концам шва.
Ручную дуговую многослойную сварку конструкций из стали 16Г2АФ толщиной более 16 мм рекомендуется выполнять с использованием так называемой мягкой прослойки. При двусторонней сварке стыковых соединений первый шов следует накладывать со стороны, противоположной прихваткам, в этом случае при обязательной подрубке корня шва прихватки удаляются.
Многослойной сваркой нередко сваривают конструкции из легированных сталей, в которых воздействие термического цикла может повлечь за собой существенные изменения свойств металла. Для таких конструкций определение термического цикла и его регулирование представляет наибольший интерес.
Многослойной сваркой обеспечивается повышенная прочность металла шва и всего сварного соединения по сравнению с однослойной: получается меньший участок перегретого металла в зоне термического влияния сварного соединения, достигается нормализация (отжиг) нижележащих слоев при наплавке последующих. Толщина слоя подбирается такой, чтобы металл предыдущего слоя приобретал мелкозернистое строение. Для сварки незакаливающейся стали толщина слоя многослойного шва составляет 3 - 8 мм в зависимости от толщины и размеров изделия. Металл верхнего слоя шва рекомендуется отжечь газовым пламенем без присадочного металла.
Схемы сварки сквозным валиком при толщине металла, мм.| Сварка ванночками. Однако многослойная сварка менее производительна и требует большего расхода газов, чем однослойная. Поэтому ее применяют только при сварке ответственных изделий. Сварку ведут короткими участками. При наложении слоев нужно следить за тем, чтобы стыки швов в различных слоях не совпадали. Перед наложением нового слоя нужно проволочной щеткой очистить поверхность предыдущего слоя от окалины и шлаков.
Определение доли участия металла в формировании шва. При многослойной сварке, когда последующий валик (рис. 66, б) накладывают в разделке па основной металл (F0 M) и предыдущий валик (Р 1 - г), их долю в образовании металла тг-го валика также следует учитывать.
Виды соединений.
К многослойной сварке короткими участками прибегают в тех случаях, когда стремятся продлить пребывание металла выше определенной температуры и не допустить быстрого охлаждения его ниже этой температуры. Тепловые воздействия навариваемых коротких слоев складываются и замедляют скорость охлаждения отдельного слоя.
При многослойной сварке каждый слой должен быть перед наложением последующего очищен от шлака и брызг металла. Дугу следует зажигать на наплавленном металле. Кратер должен заплавляться короткими замыканиями электрода. Выводить кратер на основной металл не разрешается. После окончания сварки должен быть удален грат, наплывы металла, брызги и шлак. Шлак удаляют после остывания шва.
Зависимость работы зарождения (а и работы распространения трещины (б в зоне термического влияния однослойного сварного соединения из. При многослойной сварке, особенно при автоматической под флюсом, вследствие наложения температурных полей, каждого слоя создается опасность перегрева металла.
При многослойной сварке надо так организовать работу, чтобы лосле наложения первого слоя сварщик переходил к следующему изделию или участку шва, а подручный тем временем очищал первый слой от шлака. После наложения первого слоя на втором изделии или участке шва сварщик наплавляет второй слой на первом изделии или участке шва, а подручный очищает шов на втором изделии.
При многослойной сварке надо так организовать раооту, чтобы после наложения первого слоя сварщик переходил к следующему изделию или участку шва, а подручный тем временем очищал первый слой от шлака. После наложения первого слоя на втором изделии или участке шва сварщик наплавляет второй слой на первом изделии или участке шва, а подручный очищает шов на втором изделии.
При многослойной сварке отдельные накладываемые валики должны быть по возможности одинакового сечения. Это условие диктуется необходимостью уменьшить закалку свариваемой стали в зоне термического влияния шва. Зона отпуска от наложения последующих валиков частично проходит по - зоне закалки предыдущих валиков и отпускает ее. В результате этого вся зона термического влияния может быть равномерно отпущена.
При многослойной сварке надо так организовать работу, чтобы после наложения первого слоя сварщик переходил к следующему изделию или участку шва, а подручный тем временем очищал первый слой от шлака. После наложения первого слоя на втором изделии или участке шва сварщик наплавляет второй слой на первом изделии или участке шва, а подручный очищает шов на втором изделии.
При многослойной сварке отдельные накладываемые валики должны быть по возможности одинакового сечения. Это условие диктуется необходимостью уменьшить закалку свариваемой стали в зоне термического влияния шва. Зона отпуска от наложения последующих валиков частично проходит по зоне закалки предыдущих валиков и отпускает ее. В результате этого вся зона термического влияния может быть равномерно отпущена.
При многослойной сварке надо так организовать работу, чтобы после наложения первого слоя сварщик переходил к следующему изделию или участку шва, а подручный тем временем очищал первый слой от шлака. После наложения первого слоя на втором изделии или участке шва сварщик наплавляет второй слой на первом изделии или участке шва, а подручный очищает шов а втором изделии.
При многослойной сварке нужно тщательно зачищать каждый валик от окисной пленки, характеризующейся появлением цветов побежалости. Сварку продольных швов следует начинать и заканчивать на технологических выводных планках из того же металла, что и свариваемые изделия. После окончания сварки инертный газ (подается до полного остывания нагретых участков. Техника сварки импульсной и непрерывной дугой одинакова.
При многослойной сварке после выполнения корневого шва проковывают все последующие слои.
При многослойной сварке после наложения каждого слоя необходимо зачистить шзы и свариваемые кромки от шлака и устранить обнаруженные дефекты.
Схематическое изображение работы при сварке различных. При многослойной сварке каждый слой тщательно очищают. Число слоев определяют исходя из диаметра электрода.
При многослойной сварке каждый слой ш а должен быть тщательно очищен от шлака и брызг металла; если в слое имеются поры, раковины и трещины, их надо вырубить.
При многослойной сварке после наложения каждого слоя необходимо зачистить швы и свариваемые кромки от шлака и устранить обнаруженные дефекты.
При многослойной сварке слои наплавляются поочередно с обеих сторон или же, если невозможно поворачивать изделие, сварку ведут в вертикальном положении, одновременно с двух сторон.
При многослойной сварке каждый предыдущий шов должен быть зачищен от шлака и брызг перед наложением последующего слоя шва.
При многослойной сварке каждый последующий слой ведут в направлении, обратном предшествующему, замыкающие участки каждого слоя располагают вразбежку по отношению друг к другу. Это улучшает качество сварки.
При многослойной сварке каждый слой сваривается только после остывания предыдущего. В качестве источников тока для дуговой сварки используются сварочные преобразователи, трансформаторы и выпрямители.
При многослойной сварке каждый слой тщательно очищают. Число слоев определяют, исходя из диаметра электрода.